Modules
Inventory Management
On the job site or in the warehouse, there’s no time to guess if you have the right part—or waste hours searching for it.
Yet in many companies, stock levels live in spreadsheets or people’s heads. The result? Wasted time, extra trips, and unnecessary purchases.
Inventory management needs to happen where the materials actually move—on-site, in the field, in vehicles, and across warehouses. In other words: in Kiho.
With Kiho’s Inventory Management module, products, stock levels, and transactions are all visible in one place. Whether you’re drawing from a central warehouse, a remote depot, or vehicle stock, every movement is tracked and updated in real time. You always know where your items, materials, and equipment are, who’s using them, and when.
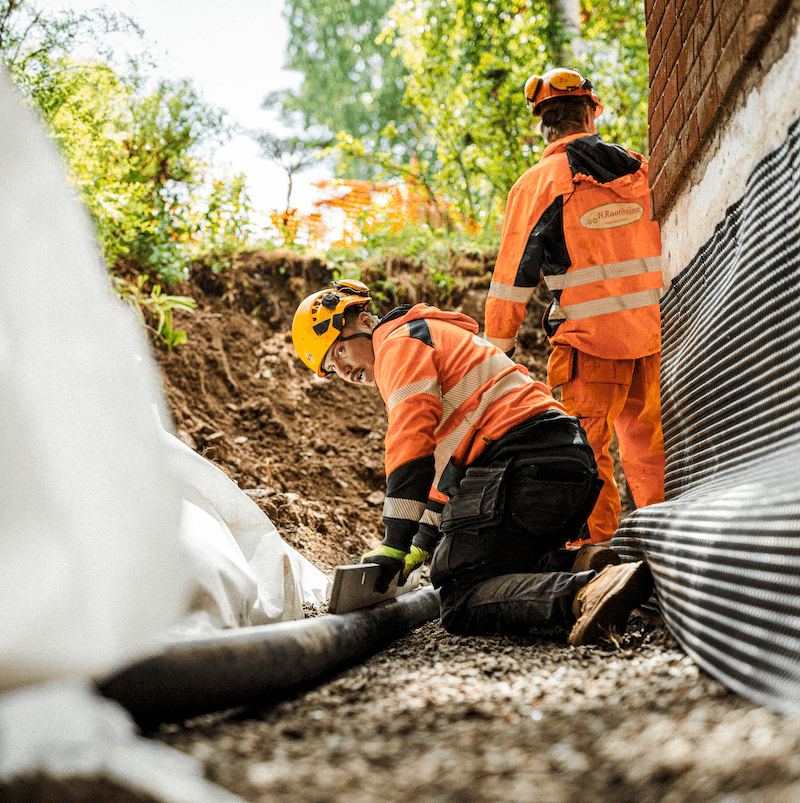
Keep your stocks in order and record usage on the job
In many companies, inventory management still relies on memory, paper slips, or scattered Excel files. As products move across job sites, stock balances often go unrecorded—or forgotten entirely. This leads to unnecessary purchases, incorrect invoicing, and in the worst cases, work coming to a halt.
Inventory management isn’t just the warehouse manager’s job. And it’s not just about inbound and outbound goods. Stock levels change the moment a technician grabs a part in the field. When usage is recorded in real time, inventory updates instantly, giving supervisors a clear view of material consumption and the ability to place additional orders in advance.
In Kiho, warehouses can be fixed, mobile, or even on-site containers. The module adapts to your company’s structure and needs, keeping your inventory under control—wherever the work happens.
How Kiho Inventory Management works in practice
1.
Record products directly to tasks or stock
All incoming and outgoing goods are logged in the app at the point of use, so you avoid errors and keep your balances up to date.
Example: A technician takes three junction boxes from the vehicle stock and logs them to the service call. The inventory count automatically decrements, and the costs are assigned to that task.
2.
Real-time stock levels across all locations
Kiho supports central warehouses, satellite depots and on-vehicle stock. Every user sees exactly what’s in each location and in what quantity.
Example: A supervisor opens the stock view to check if a specific van still has enough fittings for today’s site. If not, they can direct replenishment from another vehicle.
3.
Automatic capture of loading, unloading and transfers
Every stock movement—whether it’s a load, unload or transfer—is timestamped and recorded without extra paperwork.
Example: A driver hauls a load of crushed stone from the quarry to the jobsite. Both loading and unloading are logged in the app, and Kiho records the quantity and time—no separate forms or scribbled notes needed.
Integrate with Other Kiho Modules and Automate Everything
Kiho’s Load Tickets module works perfectly on its own, but our customers love combining it with other Kiho modules:
- Inventory Management: Real-time stock updates and full visibility into material movements
- Time Tracking: Load data logged automatically as part of daily time entries
- Invoicing: Product records that instantly generate billing data
- BI Reporting: Deep analysis of delivery volumes, material flows and task efficiency
One Kiho, one view – full control from the warehouse
Kiho’s Load Tickets module makes material flows crystal clear. It brings full transparency to deliveries and turns every load into a reliable, actionable report. Paper slips, duplicate entries, and confusion become a thing of the past—just coffee-break stories about how things used to be.
Kiho’s all-in-one application has everything you need for inventory management.
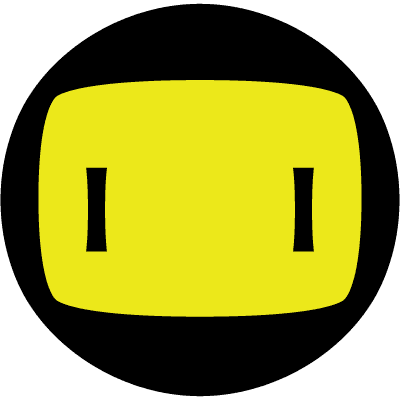